Sociedade
“Somos o MIT da Marinha Grande”
O Centro para o Desenvolvimento Rápido e Sustentado do Produto comemorou dez anos. Com um percurso de investigação de topo, articulado com grandes empresas e centros de saber, este braço do Politécnico de Leiria conta com um portfólio considerável
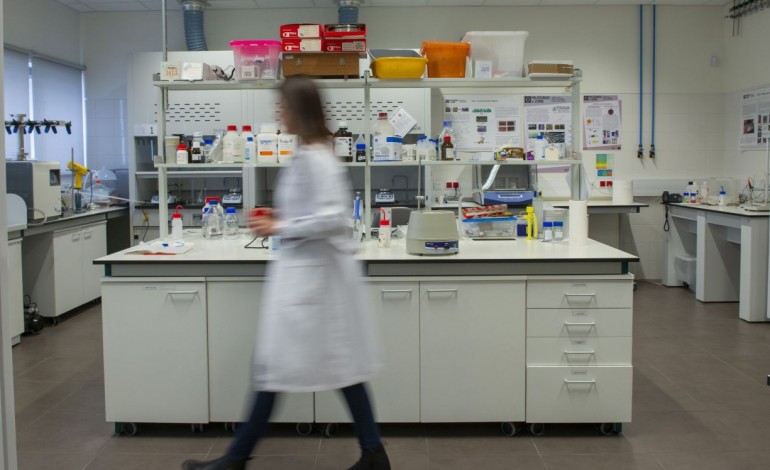
Desde as universidades inglesas mais reconhecidas, como a de Oxford, passando pelo ensino superior emergente do Casaquistão, pelos melhores núcleos de investigação nacionais, entre os quais o Centro Champalimaud, até às grandes empresas da região, como a Lusiaves, a GLN Moldes, Matcerâmica, Periplast ou Distrim2, o Centro para o Desenvolvimento Rápido e Sustentado do Produto (CDRSP) desenvolveu em dez anos um conjunto considerável de projectos arrojados, muitos dos quais com aplicação prática no mercado. O CDRSP tornou-se, de resto, no líder nacional da investigação científica sobre o fabrico aditivo.
São motivos de orgulho para a equipa liderada por Nuno Alves, actual director do CDRSP, para quem este centro, localizado na Marinha Grande, já se encontra ao nível de um MIT (Instituto de Tecnologia de Massachusetts) em pequena escala.
Parceiros de empresas em mais de 100 projectos
Mais de uma centena de projectos desenvolvidos em parceria com empresas de todo o País, e também do exterior, num valor superior a 120 milhões de euros. Esta é uma das faces visíveis do trabalho realizado pelo CDRSP numa década de actividade.
De acordo com Nuno Alves, estes projectos têm vindo a ser realizados no âmbito de quatro grandes áreas de investigação: a bio-fabricação, onde vários laboratórios produzem conhecimento na área da regeneração de tecidos, pele, osso ou cartilagem; a transformação da indústria, através da fabricação aditiva/impressão 3D combinada com as tecnologias digitais (o domínio onde o CDRSP tem o número mais significativo de projectos com relevância nacional); também a área dos materiais e processos de fabrico; e a área do desenvolvimento de métodos matemáticos e computacionais.
Uma das maiores virtudes deste centro é o contributo que tem prestado junto da comunidade. Cerca de 70% dos projectos desenvolvidos com as empresas têm forte impacto em termos de aplicações médicas e das áreas sociais, realça Nuno Alves.
E na medida em que a presente transformação da indústria conduzirá a uma revolução nos processos de fabrico, além de desenvolver novas formas de projectar e de produzir produtos, o CDRSP também se preocupa em formar recursos humanos para que estes tenham qualificações ajustadas às futuras necessidades das empresas, explica o professor.
O director do CDRSP refere- se aos cursos de mestrado e mais concretamente ao novo programa doutoral desenvolvido em articulação com a Universidade do Minho, e que o centro irá submeter a aprovação ainda este mês.
O trabalho assente numa equipa de investigadores que é jovem e internacional cria de resto um ambiente de ideias novas e disruptivas, salienta o responsável pelo centro.
Entre 2013 e 2017, exemplifica o responsável, trabalharam 250 jovens investigadores no CDRSP. E durante esses mesmos cinco anos, repara o director, 10% das pessoas que ali pesquisavam eram estrangeiros; 80% dos docentes integrados tinham experiência em trabalho internacional; e 60% da equipa tinha experiência em investigação internacional.
Tais características têm vindo a gerar projectos inovadores, nota Nuno Alves, que deixa vários exemplos.
Vestuário que mede sinais vitais
Com o apoio da FCT, o CDRSP está a desenvolver um projecto que pretende investigar métodos de produção de sistemas micro-eletrónico- mecânicos (MEMS) flexíveis em pequena e grande escala.
Na prática, trata-se de uma tecnologia que se pode vestir, que pode ser acoplada à pele humana e acompanhar os seus movimentos, podendo detectar sinais vitais ou a actividade muscular, resultando em equipamentos de monitorização da saúde.
Algas para aumentar tempo de vida de alimentos embalados
A Periplast, em conjunto com a Lusiaves, o instituto Nacional de Saúde Dr. Ricardo Jorge, a GLN Moldes e o CDRSP estão a desenvolver o prjeto iFILM, com vista ao desenvolvimento de um novo artigo/ processo de fabrico de filmes termoplásticos ultrafinos. Na prática, este projecto pretende utilizar, entre outros materiais, extractos de macroalgas marinhas para o fabrico das nanofibras, que possam ser usadas na produção dos filmes termoplásticos ultrafinos. Atendendo às suas propriedades antioxidativas, estes poderão contribuir para o aumento do tempo de vida dos produtos embalados.
O robot que imprime órgãos humanos
O uso de robots na medicina tem ganho cada vez mais força. Estes, em conjunto com o uso da tecnologia aditiva para a produção de substitutos biológicos, irão marcar uma nova era na medicina. Este projecto, designado printONorgans, que conta com o trabalho conjunto da Biosckin, Molecular and Cell, Therapies,CDRSP, AMCubed, Universidades do Porto e de Coimbra, pretende trazer estas tecnologias de lab o r at ó r i o para o ambiente hospitalar, desenvolvendo um robot para impressão directa in situ de materiais em tecidos e/ou orgãos danificados, de forma costumizada e pouco invasiva.
Lã e madeira para fazer peças automóveis
A Distrim2, juntamente com a ATT - Advanced Tool Technology, o CDRSP e a Universidade de Coimbra, está a trabalhar no projecto WoWW, que tem por objectivo desenvolver materiais, processos e produtos inovadores baseados em materiais compósitos constituídos por matriz termoplástica reforçada com fibras híbridas de lã e de madeira.
Entre outras finalidades, o projecto propõe aplicações para a indústria automóvel e para a área da saúde, exigindo uma cadeia de desenvolvimento tecnológico para a sua produção e aplicação nestas áreas estratégicas da economia.
As principais motivações subjacentes a este projecto baseiam-se nas vantagens ambientais comuns aos materiais compósitos que utilizam fibras naturais de reforço, acrescidas das vantagens particulares da lã, em virtude das suas propriedades intrínsecas, contribuindo para ultrapassar algumas limitações dos compósitos que já contêm fibras vegetais.
Copos e vasos feitos por impressão
Add.Vitrum é um projecto de fabrico digital de produtos em vidro, que está a ser realizado num consórcio liderado pela Vidromecânica, e que conta com a parceria de AMCubed, BF Glass Studio & Gallery, Favicri, Universidade do Minho, Normax e o CDRSP. O projecto surge na tentativa de aliar a tradição e a inovação em prol do fortalecimento económicoda indústria vidreira (vidro utilitário, artístico e técnico), outrora um dos p r i n c i p a i s clusters industriais da região de Leiria. De forma a colmatar esta lacuna, a Add.Vitrum pretende produzir peças de vidro através do fabrico digital directo, usando uma metodologia abrangente que integra várias abordagens de fabrico, desenho, controlo, gestão, informação e comunicação e outras interligadas em rede e em consonância com as da 4ª revolução industrial.
Já o Direct.ceramic é um projecto que consiste na investigação e desenvolvimento de novas tecnologias produtivas baseadas em fabrico aditivo para produtos cerâmicos. Está a ser desenvolvido num consórcio liderado pela Matcerâmica, envolve o CDRSP e o Kerajet, e assume que a exploração de novas técnicas de fabrico e sua inserção em sistemas industriais sustentáveis permitirão ao sector ganhos de eficiência, bem como a expansão do seu leque de soluções e produtos, e com isso a aproximação dos clientes finais.
Sepulturas em cortiça
Disponível para parcerias está o projecto Cork Graves, que consiste num conjunto inovador de campas em cortiça, aplicada sobre uma estrutura em aço. “A escolha do material foi fácil. Nobre, sustentável, versátil e leve, a cortiça saltou do mundo do vinho para se revelar uma das matérias-primas de eleição deste século, sendo uma mais-valia competitiva no mercado actual”. Adicionado à simplicidade de suas formas, este material “permite a desejada integração das Cork Graves com a natureza, como que fazendo parte da paisagem”, nota o centro de investigação.
Eléctricos movidos a bateria eléctrica
No âmbito de um curso de mestrado em design de produto, um grupo de alunos do CDRSP e da FA-UTL (Faculdade de Arquitectura da Universidade Técnica de Lisboa) concebeu o Eléctrico Panorâmico, um projecto desenvolvido a pensar no percurso da carreira 28 da Carris, em Lisboa. Trata- se de “um percurso com uma elevada sazonalidade, ocorrendo principalmente durante os meses de Verão, época em que os turistas enchem os eléctricos para percorrerem a zona histórica da cidade”. O que torna este eléctrico singular é o facto de ter sido projectado com duas áreas de estar distintas, uma para percursos mais prolongados no piso superior, proporcionando também uma vista mais panorâmica, e outra para passageiros habituais no nível inferior, com acesso a pessoas com mobilidade reduzida.
Do pré-fabricado aos laboratórios
O CDRSP teve a sua génese na Escola Superior de Tecnologia Gestão (ESTG) do Politécnico de Leiria (IPLeiria). O actual director do CDRSP foi um dos jovens que esteve envolvido na sua formação e diz que é preciso recuar alguns anos para perceber a importância do aparecimento de um centro desta natureza.
Na década de 90, os professores não pensavam muito em investigação, muito menos na relação que a academia poderia ter com as empresas. Foi preciso esperar alguns anos até que no Departamento de Engenharia da ESTG se começasse a pensar em orientar as primeiras investigações no âmbito dos mestrados, recorda Nuno Alves.
Contudo, enquanto escola de politécnico, a ESTG não podia conferir esse grau. Foi nesse momento, para poder ministrar o mestrado, que a ESTG e o IPLeiria estabeleceram uma parceria com a Universidade do Minho. Com a chancela da universidade, as aulas do mestrado em Engenharia Mecânica e Desenvolvimento de Produto passaram a decorrer na ESTG, e os docentes de Leiria passaram a envolver- se nas orientações das teses.
E para dar resposta à nova realidade, muitos docentes realizaram as suas próprias investigações de doutoramento, explica Nuno Alves.
Foi neste contexto, em 2006, que um grupo de docentes da ESTG, entre os quais o coordenador do Departamento Engenharia Mecânica, Paulo Bártolo, também Nuno Alves e Artur Mateus, começaram a organizar-se para fazer investigação diferenciada, direccionando a sua atenção para a prototipagem rápida, que evoluiu para fabricação aditiva, e que hoje inclui impressão 3D e tecnologias digitais.
No ano seguinte, o grupo decidiu submeter este núcleo de investigação a avaliação por parte da Fundação para a Ciência e Tecnologia (FCT). E em 2008, já com a designação de Centro para o Desenvolvimento Rápido e Sustentado do Produto, o centro obteve a melhor das classificações atribuídas pela FTC, um excelente, que lhe valeu, da parte de Luciano Almeida, então presidente do IPLeiria, a constituição do CDRSP como unidade de investigação orgânica, com autonomia administrativa.
O CDRSP foi assim formalmente constituído em 2009, ficando a funcionar na ESTG, até ser transferido para pré-fabricados, junto ao hospital de Leiria. “Foi o nosso primeiro espaço. Mas tínhamos a ambição de ter um edifício próprio, com laboratórios mais adequados à actividade que tínhamos traçado”, aponta o director.
E foi uma óptima oportunidade quando o IPLeiria e a Câmara da Marinha Grande estabeleceram um protocolo, que cedia instalações no Centro Empresarial da Marinha Grande e também uma propriedade contígua, que poderia ser usada se o CDRSP se expandisse.
Essa expansão concretizou- se e o CDRSP funciona desde 2016 em instalações próprias, com laboratórios ajustados ao desenvolvimento de ciência de topo.
Centenas de publicações científicas
Além das instalações, avolumou-se a equipa e o número de projectos desenvolvidos no CDRSP. Em dez anos de actividade, o centro desenvolveu mais de um centena de projectos com empresas, perfazendo um total de 120 milhões de euros.
E de acordo com os últimos dados apresentado à Fundação para a Ciência e Tecnologia, entre 2013 e 2017, o CDRSP contava com 17 docentes doutorados integrados, mais dez não integrados, cinco bolseiros com doutoramento e mais 40 outros bolseiros com licenciaturas e mestrados.
Entre 2013 e 2017, o CDRSP foi também responsável por 200 publicações, 70% das quais em revistas científicas de topo e contou com a participação de 98 investigadores a ministrar palestras plenárias internacionais. Só em 2018, o Centro participou em 46 publicações científicas. Além das centenas de empresas que têm sido parceiras de projectos do CDRSP, o centro conta actualmente com cerca de 50 parceiros académicos, entre universidades nacionais e estrangeiras.
Produtos chegam ao mercado. Mas as patentes não
Ao longo de uma década de actividade, o CDRSP já terá sido responsável por cerca de uma vintena de projectos/ produtos patenteados. Mas nenhuma empresa comprou uma única patente. Nuno Alves explica que existem duas grandes justificações.
Em primeiro lugar, nunca surgiu nenhum contrato onde ambas as partes acordassem sobre os valores das royalties. Por outro lado, os tempos da ciência e das indústrias são muito diferentes e acontece frequentemente estar a ser desenvolvida uma ideia que terá aplicação a médio prazo, mas que corre o risco de, quando finalmente puder ser fabricada, já ter sido ultrapassada por uma outra tecnologia que mais convém à empresa fabricante, expõe o director do CDRSP.
Mas a falta de patentes não tem impedido que muitos dos produtos desenvolvidos pelo centro, em articulação com as empresas, cheguem ao mercado, salienta o responsável pelo CDRSP. “Nesses projectos, de co-promoção, liderados pelas empresas, faz-se muita transferência de conhecimento”, prossegue o director.
A tendência para a substituição do plástico é outro tema sobre o qual temreflectido este centro de investigação. Nuno Alves considera que este fenómeno não tem nem terá impacto negativo sobre a actividade do CDRSP, na medida em que este tem procurado desenvolver produtos sustentáveis.
São disso exemplo os projectos de aproveitamento de borracha em fim de vida, de serradura, ou reciclagem de polímeros e sua reintrodução na cadeia produtiva. Além disso, realça, a impressão 3D, que é a grande bandeira deste centro de investigação, implica muito menos desperdício de recursos do que as tecnologias convencionais, onde é necessário fazer um molde, maquiná-lo, injectar plásticos, utilizando canais e outros sistemas que são desperdício.
E como gostaria de encontrar o CDRSP daqui a dez anos? “A trabalhar com os melhores”, responde prontamente Nuno Alves. “Já somos um MIT a uma escala reduzida. É assim que já vejo o CDRSP há uns anos. Somos o MIT da Marinha Grande. É claro que temos mais dificuldades quando há transição de quadros comunitários, mas temos mais autonomia financeira, e essa é também a ventagem de sermos mais pequenos”, repara o director.